Researchers in the Virgina Tech College of Science have developed a material that is up to 40 times faster in desalinating small batches of water than other materials available today. This material is composed of long, fibrous strands of carbon with uniform mesopores of approximately 10 nanometers. Guoliang Liu, an assistant professor in the Department of Chemistry, has been researching the design and synthesis of porous carbon fibres for the last several years.
According to Liu, his porous carbon fibres could find application in the automotive industry, where similar, but less efficient, materials are already used as the external shells of some luxury cars. Now, Liu reports a new application for this material: capacitive desalination.
“Because of the high surface area of the porous carbon fibres, we can store a lot of ions,” said Liu. “Because of the interconnected porous network, the ion movement is very fast inside the pores.”
Desalination and capacitive desalination process
The most well-known method of desalination is reverse osmosis, in which seawater is forced through a semi-permeable membrane to separate salts from water. Liu said the materials and process in reverse osmosis are relatively mature now, and this energy-intensive process is efficient at treating large quantities of water. Capacitive desalination using porous carbon fibres, on the other hand, requires much less energy for treating water with low salinity.
“The advantage of our process is that we can have much faster, much higher capacity, and more energy efficiency at this concentration range,” Liu explained. “Under our experimental conditions of around 500 milligrams (of salt) per liter, it’s going to be way more expensive if you use other means because you’re trying to get a little bit of salt out of the water.”
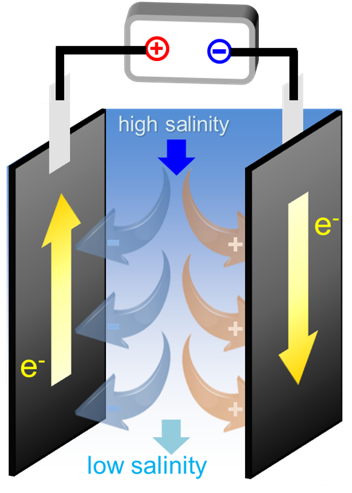
According to Tianyu Liu, a postdoctoral research associate in the Liu Lab, the process was simple: he placed two pieces of porous carbon fibres into a saline solution, and then he applied a voltage through the fibres. This applied voltage created an electrostatic force that naturally attracted the salt ions out of the water.
“Capacitive desalination treats the water using electrodes with high surface areas and electrical conductivity,” Tianyu Liu said. “The potential you apply reduces the ion concentration in water, and then you discharge the ions to regenerate the electrodes. These processes are repeatable with negligible loss of desalination capacity.”
Next steps of the research
Tianyu Liu notes that while this material has shown great results, the research team has only shown a proof of concept for desalination. They are looking for engineering laboratories on campus and across the country to help scale up this research and design large-scale desalination cells. GuoliangLiu’s porous carbon fibres are promising for end applications as diverse as batteries, cars, and desalination, and maybe the material could have further applications.
An article detailing this work was published in Science Advances.
Featured image: Tianyu Liu is a postdoctoral research associate in the lab of Guoliang “Greg” Liu, an assistant professor in the Department of Chemistry.
Fig. 1: A capacitive desalination cell works when a power source applies a constant potential between two electrodes, making one electrode positively charged and the other negatively charged. The positively and negatively charged electrodes adsorb anions and cations, respectively, through electrostatic adsorption. Meanwhile, electrons flow out from the positively charged electrode and enter the negatively charged electrode to maintain the charge neutrality on the electrode surfaces. These processes decrease the salinity of the treated water. Credit: Science Advances.
Source: Virginia Tech