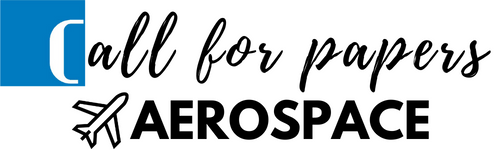
A PocketQube is a type of miniaturized satellite for space research that usually has a size of 5 cm cubed (one eighth the volume of a CubeSat), and a mass of no more than 250 grams. This type of satellites is quite young – started in 2009, with the original idea from Professor Robert J. Twiggs, Morehead State University (MSU) – and their importance is increasing at warp speed, as a solution to the rising costs of CubeSat launches to low Earth orbit. The first PocketQube Standard has been issued in June 2018, providing a shared platform to the PocketQubes community; one of the contributors (along with GAUSS Srl, TU Delft) is Alba Orbital, a fast growing high-tech SME based in Glasgow, Scotland.
Challenge
Recently Alba Orbital needed to build an updated version of their PocketQube satellite deployer, AlbaPod.
The aims of the project were to improve on previous designs in terms of:
- weight
- manufacturability
- access
- and incorporate a number of safety features.
Alba Orbital turn to CRP Technology for the manufacturing of the deployer, as the Italian-based 3D printing company built a considerable experience supplying cutting-edge solutions for space key industry leaders using its patented Windform® TOP-LINE composite materials. In fact most of Windform® TOP-LINE composite materials are suitable for space applications and have passed outgassing tests at NASA and ESA.
As with any aerospace part, minimizing weight is a fundamental design goal, additionally it is essential that the material has been approved for flight due to tight rules regarding degassing once in space.
Solution
Selective Laser Sintering and Windform® XT 2.0 Carbon fiber filled composite material were chosen as manufacturing process and construction material.
Alba Orbital team say, “as the product needed to withstand a launch to space while containing several satellites, the pod needed to withstand high vibrations, and in the worst scenario, contain any satellite that breaks free internally. Windform® XT 2.0’s toughness and strength make it a perfect candidate for this use case.”
In the composite materials for Additive Manufacturing scenario, Windform® XT 2.0 features important mechanical properties including
- 83,84 Mpa tensile strength
- 8928,20 Mpa tensile modulus
- 3,80% elongation at break
- 76,43 UST per density unit.
Result
The result was AlbaPod V2, an extremely light weight 6P (up to 6 satellites) 3D printed deployer for PocketQube compatible satellites, with a mass of <500g (60% less than AlbaPod v1).
Professional 3D printing, combined with Windform® XT 2.0 Carbon-composite material, proved to be the best manufacturing choice: the 3D printed deployer has successfully passed the control criteria, and has fully complied with the requests and Alba Orbital’s standards.
Alba Orbital team add, “Windform® XT 2.0 is a non-outgassing, lightweight fibre reinforced polyamide plastic very similar to Nylon. The material combined with the manufacturing technique allowed us the option to design parts that can not be manufactured with traditional techniques, with thin sections and extremely complex geometry’s, and these parts can be manufactured and delivered in a fraction of the time for a traditional supply chain.”
Alba Orbital team specifies some technical details the advantages obtained by using Additive Manufacturing and Windform® XT 2.0 material: “The most innovative aspect of the project was the sheer number of components we switched over to Windform® XT 2.0, not only was the shell redesigned in the material, but also the moving ejection mechanism and door assembly. Additionally some parts are critically structural to the assembly as a whole.”
Regarding the mechanical performance of this part, they say that “this is critical. Not only does the full assembly need to function correctly to facilitate the deployment of the satellites inside, but must also contain the satellites in the event of catastrophic failure of a payload during the launch as anything breaking free could fatally damage other payloads or the launch vehicle itself. This was tested thoroughly with free masses on vibration tables at extremely high loading and the shell held up phenomenally.”
“Additionally weight – Alba team specifies – is a major concern with anything going into space due to the costs associated, utilising Windform® XT 2.0 allowed us to reduce the mass of a number of major components.”
Alba Orbital team foresee and hope for an increasing use of professional 3D printing in the field, because, they say, “3D printing allows us to rapidly improve design and customise/create bespoke launchers in the future for demanding payloads which may fall outside the PocketQube standards or require special considerations. It will also allow the fast integration of new release mechanisms allowing us to switch manufacturers comparatively quickly and easily if problems with supply chain arise.”
Alba Orbital team performed many tests on the 3D printed AlbaPod v2.
On September 9th 2019 the first PocketQubes integration occurred.
At the beginning of December 2019, Alba Orbital launched 6 PocketQube satellites into orbit via the 3D printed AlbaPod v2 (mission: Alba Cluster 2). Alba Cluster 2 stayed on orbit for 100 days.
So far AlbaPod v2 has completed four missions and has launched to orbit 25 PocketQube payloads. Last launch was with Space X’s Transporter-6 mission occurred 3rd January 2023.